For part 4 of this limited series, I share a somewhat lesser-used maker material, one I've grown steadily to depend on. It's a type of plastic, so I never buy new, instead preferring to search the scrap bins outside my local plastics fabrication shop.
Happy Friday, all. And happy making. ~JRC
Today's featured material: reclaimed high-density polyethylene sheets.
Tools I use: almost anything used in woodworking works great with HDPE, including the table saw, circular saw, and various other related tools.
Cost of entry: Depending on the build, you'll need basic cutting and drilling equipment ranging from inexpensive hand tools to costly shop equipment. (Starting with HDPE is effectively free for the already equipped woodworker.) The HDPE sheets, commonly between 1/4" and 1/2" thick, can be had on the cheap, often for around $2/pound if sourcing off-cuts and scraps from a local plastics fabricator.
"[C]reating a more sustainable relationship with plastics will require a new dexterity on our part. It will require us to think about the entire life cycle of the products we create and use."
― Susan Freinkel, Plastic: A Toxic Love Story (2011)
Plastics have gotten a [much deserved] bad rap in recent decades due to their grave environmental toll, including heavy fossil fuel consumption in manufacturing and planet-scale post-production contamination. Today, it's safe to say nary a square inch of Earth is safe from microplastics. That said, plastics have great utility and have revolutionized modern life in many ways for the good. But plastics, like any material with a high environmental cost, must be used wisely.
Of all the polymer formulations for plastics, one stands out in its ubiquity and broad utility: high-density polyethylene, or "HDPE" for short. This plastic has an incredibly high strength-to-density ratio making it excellent for wide-ranging applications from bottles to envelopes, clothing to toys, and pipes to medical instruments.
If you have a plastic item nearby, it's likely some version of HDPE.
Unfortunately, many of these uses are disposable or one-off in nature (e.g., plastic bags - yuck). But on the flip side, HDPE is one of the more readily recycled plastics. As such, a lot of HDPE products are already made from post-consumer recycled material (rather than virgin plastic made newly from oil). And one of the best applications of recycled HDPE is in the form of thick, durable sheets, like those used in plastic cutting boards.
HDPE sheeting (the thicker stuff ranging from 1/4" to over 1/2" thick) is an excellent surface material for counters, decks, and other comparable uses. While HDPE sheeting is widely used for the aforementioned cutting boards, far better materials exist for this purpose (namely, hardwoods like maple or walnut). But HDPE is exceptional in harsh conditions, such as marine applications. Other materials like metal and wood suffer in these saline environments, but not HDPE. Some formulations even have UV stabilizers in them, making them suitable for almost any outdoor application.
I possibly (looks both ways before continuing) have re-purposed an old cutting board or two into something better. But most of the HDPE sheets I use are those from the scrap heap destined for recycling. It's far less energy-intensive to reuse material than to recycle it, so I feel better about my plastics use as a result.
I often utilize HDPE sheets where I normally would reach for wood. The material adds a nice contrast in my designs and can make the ordinary look surprisingly special. Bonus: HDPE comes in a rainbow of colors, not just that milky white (its natural shade). I have some red sheets, a nice selection of black ones, and even a coral-orange sheet I am itching to design something around.
As I sit and type this essay, I can see at least six items I’ve made from HDPE sheets. These include a set of shelves by my central workbench, another shelf for my power supply and soldering station, two separate pairs of "soft jaws" for my shop vises, a magnetic hook I hang my magnifying visor on, and the decks on my welding cart.
I tend to think of HDPE sheets much in the way I do plywood - the stuff works great for flat surfaces, like shelving and similar storage applications.
But it can also be machined easily, so I try and dream up more elaborate uses. Those two pairs of soft jaws and the hook all required a small degree of shaping using the router, for example.
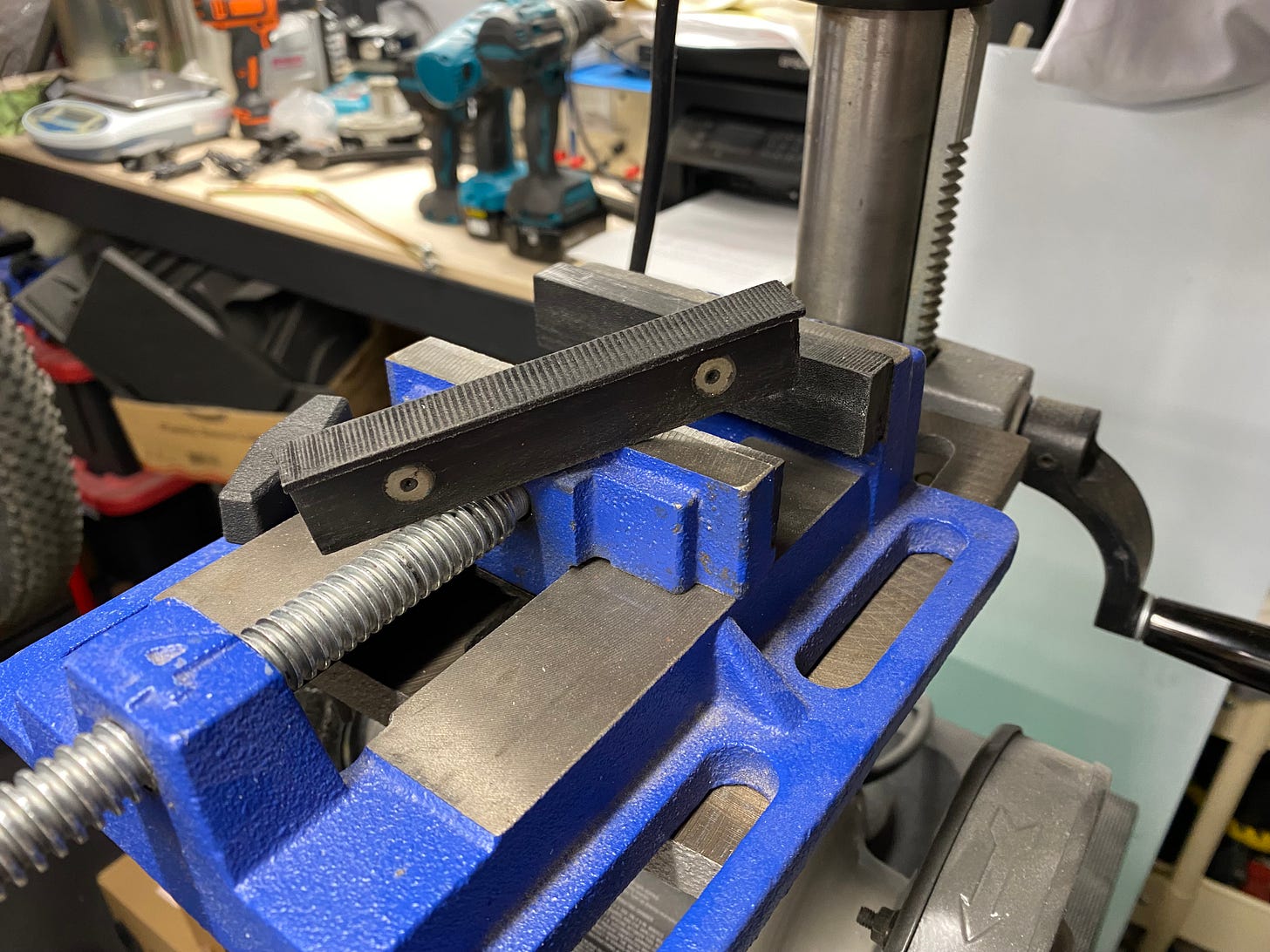
HDPE sheeting cuts beautifully on the table saw (and the router), but this plastic is soft enough to cut by hand too. And it drills nicely, of course. Whenever you cut or drill, do go slow. The material will melt and deform at higher speeds. If accuracy is critical, I sometimes lubricate with water while drilling a hole in HDPE.
HDPE sheeting does have a few quirks that must be considered when using it, especially if it's a wood replacement.
For one, it does bend, even the thick stuff, so it's unsuitable for spanning great distances alone. The two-foot-long shelves beside my bench pushed the limits of the 1/2" HDPE I used; they sag a little in the middle. This doesn't mean you can't use HDPE sheets for such applications, but reinforcing with cross members, braces, or gussets is a good idea.
Another primary consideration when using HDPE is that you can't glue it. Seriously, no adhesive known to science will hold HDPE. And I've tried several, including CA ("super") glue, two-part epoxy, contact cement, and more. Why did I try so many? Because I failed to read the fine print for HDPE, which reads: glue doesn't work, so don't bother.
Instead, mechanical connections are essential when making with HDPE. Screws, either wood or machine screws, work exceptionally well. I've even cut threads into HDPE before.
Pressure-fit connections also work well.
When you create two parts that mate together, make the one inside slightly too big, which causes the parts to wedge together and stay put. I stuck magnets into the back of the soft jaws and hook this way. And the hook is two-part, with the "hook" piece fitting into the base via a grove cut slightly less wide than its mate.
One final note on using HDPE: be mindful of the chips and dust you create when sawing and shaping it. These need to be collected separately from other shop waste and, if possible, recycled. I've yet to find a local recycler that will take plastic shavings, but I keep searching. (I don't want to be the guy adding more of this stuff into our environment.) If you have any tips on collecting and recycling small bits of plastic, please share them in the comments.
Okay, there you have it - another one of my favorite go-to maker materials. Unlike wood and metal, HDPE sheets are not as commonly used in the shop. But if you try making something with this versatile plastic, I am sure you'll see the merits of HDPE.
The stuff is way too good for plastic bottles and bags.
Until next time.
JRC
Hi John,
A fun read as always.😊😊😊
In the medical device industry I worked quite often with HDPE. We actually were able to bond it, but it required either heating with a torch, or sanding, to create the bondable surface. Here’s a link that talks a little bit about how that can be accomplished.
https://www.hunker.com/12561365/how-to-glue-hdpe
Very interesting ! and very good ideas for using HDPE